2020年6月30日星期二
Paneled Doors and Walls
from FineWoodworking https://ift.tt/31tEFGE
High-quality Hardwood
Some of you may know that Woodworker’s Journal has a group of online folks who have volunteered to be surveyed about various woodworking topics.
Recently one small part of a survey asked about the challenge to getting good-quality wood for project building. That struck a nerve with me, and I wanted to ask our Weekly readership if that is your experience, too.
Generally, are you having increased difficulty finding good-quality hardwood or other species to use in your shop? Is the quality of the wood available your challenge, or are you demanding better stock than you have previously? Let me know what you think. After all, you can’t do woodworking without wood!
Rob Johnstone, Woodworker’s Journal
Veneering with a Vacuum Pump
A vacuum pump and veneer bag is a fully portable system that can be used anywhere. Here, learn some simple veneering techniques.
Cutting Bowl Blanks from a Tree
Dale Larson from the American Association of Woodturners takes you through the best methods for harvesting bowl blanks from a tree, and how to maximize your chances for getting the grain patterns you want.
From Our Sponsor
How many clamps does a woodworker need? Probably a few more! Clamps have all kinds of uses in a shop setting, and when you need ’em, well, you REALLY need ’em! The video below explores and explains some of the basic types and common applications of various clamps. |
15% OFF: Excludes gift cards, product bundles with gift cards or free products, power tools, Porter-Cable dovetail jigs, CNC machines, Leigh products, SawStop, Festool, Tormek, Ready2Rout, select Rockwell products, taxes, Apollo sprayers, shipping charges, sale items and other promotions. Other exclusions may apply.
FREE SHIPPING: $39+ Orders. Additional shipping charges will apply for select oversized items, express orders, international orders, and orders to Alaska, Hawaii, Guam, Puerto Rico, and the Virgin Islands. Rockler reserves the right to limit quantities, correct errors or omissions and modify or end this promotion at any time. Neither 15% off nor FREE SHIPPING can be combined with any other offer or applied to previous orders. Not valid with Rockler’s Professional Catalog and independent resellers. Offer ends 7/2/20.
The post High-quality Hardwood appeared first on Woodworking | Blog | Videos | Plans | How To.
from Woodworking | Blog | Videos | Plans | How To https://ift.tt/3eMLdE7
Grind and get back to work – fast
from FineWoodworking https://ift.tt/3gbAKCn
What Will You Learn Next?
In response to Rob’s inquiry last week about what new things you’d like to learn next in your woodworking hobby, here’s what several have shared. – Editor
“I’ve tried just about every type of woodworking except for turning. I’ve debated for years about whether I should buy a lathe. I keep pretty busy working on other projects, but turning has always fascinated me. I just don’t know if I want to spend the money on a lathe and all of the accessories that go along with it. I should probably decide pretty soon, because I’m not getting any younger!” – Carol Johnston
“I have a little single-car garage, and in July I am going to have a ‘L’-shaped garage built. I will be challenged to set it up so I can actually do things in it.” – Dave Phelps
“I am trying to get better at using hand planes.” – Rudy Gonzalez
“I’m getting old. It is time I learned how to build a small deck with a wheelchair ramp off of it — just in case.” – RileyG
The post What Will You Learn Next? appeared first on Woodworking | Blog | Videos | Plans | How To.
from Woodworking | Blog | Videos | Plans | How To https://ift.tt/3igPYrG
2020年6月29日星期一
Uprooted Red Oak Recovery | Urban Logging
from Matthew Cremona https://www.youtube.com/watch?v=EI5F_RY9irA
When a dowel joint breaks
from FineWoodworking https://ift.tt/2Zd27VG
2020年6月28日星期日
2020年6月26日星期五
Chair Kits, Dressing Vanity, Workbench Kits Update
from Matthew Cremona https://www.youtube.com/watch?v=0mt7BpWLSWo
Charcooties Board
Show Notes coming soon.
The post Charcooties Board appeared first on The Wood Whisperer.
from The Wood Whisperer https://ift.tt/2BFWMOH
It’s time Thomas Day took his place alongside Townsend, Phyfe, and the others
from FineWoodworking https://ift.tt/31gP4W5
DIY Electromagnet | Vise For Excelsior Drill Press
from Black Beard Projects https://www.youtube.com/watch?v=e_ua18J8NOg
"You Can't Make That From Plywood"! Oh, Yes I Can.
from John Heisz - I Build It https://www.youtube.com/watch?v=G4TnBqM9yhY
2020年6月25日星期四
Improved Project Dollies
Mover’s dollies can come in handy for moving large projects around the shop when working alone, but their narrow top frames and carpeted surfaces would often cause my projects to slip off. So I replaced the carpet with a piece of 3/8″ plywood and stapled a section of foam mat on top of it. The plywood adds surface area and the mats resist slipping.
– Steve Meyer
Defiance, Missouri
The post Improved Project Dollies appeared first on Woodworking | Blog | Videos | Plans | How To.
from Woodworking | Blog | Videos | Plans | How To https://ift.tt/3i22Od9
2020年6月24日星期三
My imgcomp motion triggered timelapses program
from Matthias random stuff https://www.youtube.com/watch?v=ztSH9vYAIcM
IMPORTANT: How woodworkers injure their hearing and eyesight
from Stumpy Nubs https://www.youtube.com/watch?v=GrGHtM4hZoM
Tool Review: Wagner Orion 950 Pinless Moisture Meter
from FineWoodworking https://ift.tt/37XcuAX
Level up your drill press
from FineWoodworking https://ift.tt/2A3nxfC
2020年6月23日星期二
What you need to know about your woodworking router's speed
from Stumpy Nubs https://www.youtube.com/watch?v=YezRMbWTfC8
Workshop Tip: Add a door handle to your router-table push block
from FineWoodworking https://ift.tt/3hUfSkS
Woodworking is All That
The term “woodworking” is both specific and broad. Framing carpenters are certainly working with wood every day, and scroll saw experts are too. You get the picture — woodworking constitutes a great many possibilities. The feedback I received from our Weekly crowd about kits a couple of weeks ago spurred some thoughts on the subject. Readers indicated that kits can be an entry point into a new type of woodworking. And a recent survey we conducted indicates that 38 percent of those queried had used this pandemic period to learn something new about this broad craft. That got me wondering about what aspects of woodworking you are interested in learning. What are you hankering to take on next? Send in your thoughts and we will share what we can in the Feedback section.
Rob Johnstone, Woodworker’s Journal
Finishing Outdoor Furniture
What’s the difference between interior and exterior varnish? . Our expert presents several options for exterior finishes – including leaving the wood au naturel.
Project: Yard Tool Organizer
This fast and easy project gets your long-handled yard tools off the floor and helps organize your garage and keep it clean.
From Our Sponsor
If you want a silky-smooth finish on your next project, there’s a simple way to achieve it! Our Skill Builder video takes you through the process of filling wood grain to put your project on the fast track to the smoothest possible finish. |
15% OFF: Excludes gift cards, product bundles with gift cards or free products, power tools, Porter-Cable dovetail jigs, CNC machines, Leigh products, SawStop, Festool, Tormek, Ready2Rout, select Rockwell products, taxes, Apollo sprayers, shipping charges, sale items and other promotions. Other exclusions may apply.
FREE SHIPPING: $39+ Orders. Additional shipping charges will apply for select oversized items, express orders, international orders, and orders to Alaska, Hawaii, Guam, Puerto Rico, and the Virgin Islands. Rockler reserves the right to limit quantities, correct errors or omissions and modify or end this promotion at any time. Neither 15% off nor FREE SHIPPING can be combined with any other offer or applied to previous orders. Not valid with Rockler’s Professional Catalog and independent resellers. Offer ends 7/2/20.
The post Woodworking is All That appeared first on Woodworking | Blog | Videos | Plans | How To.
from Woodworking | Blog | Videos | Plans | How To https://ift.tt/2Z4DA54
How To Make A Power Hacksaw Machine Part-2 || DIY Power Hacksaw
from Mistry MakeTool https://www.youtube.com/watch?v=sLq6l4Rjvl0
DIY Workbench // mobile and multipurpose (I needed this)
from DIY Creators https://www.youtube.com/watch?v=_ravTLhvBhw
2020年6月22日星期一
The mighty pipe clamp
from FineWoodworking https://ift.tt/3hNz7MS
2020年6月21日星期日
Mud Kitchen
The best part of the kitchen is the sink! Right?
My kids have always loved play kitchens, and I've built many. But not having a working sink with real running water always required alot of imagination.
Then I discovered the MUD KITCHEN!!!
Mud Kitchen Features
- Real working sink that hooks up to a garden hose
- Faucet cannot be left on - automatically turns off when not actively in use
- Drain water can be reused
- Hooks for storing pots, pans and utensils
- Removeable "stove" pieces to customize use (ie use as a potting bench or rock cleaning and paint station)
- Storage shelf
- Easy to customize and decorate
- Sturdy construction using time tested methods suitable for outdoor use
- Cedar flat surfaces will last longer
- About $50 in new materials to build
- Simple construction that most anyone can tackle with a few tools
We LOVE this mud kitchen as is, but I did want to mention my six year old son thought it would make a fantastic fish cleaning station. He also is washing rocks and painting them. I could also see this used as a child's potting bench, serving area for kids, lemonade stand, or wildflower florist station. The options are endless!
Video Tutorial
I did a video tutorial of this build, please take a moment to watch before you tackle this project:
Mud Kitchen Plans
The mud kitchen plans follow, please share a photo if you build - we love seeing your projects.
from Recent Project Plans https://ift.tt/313uloE
Shop Made Drawer Pulls
from Jay Bates - Woodworking Videos https://www.youtube.com/watch?v=8N3s4wK-LHk
Making Vertical Blinds with Exposed Mechanical Linkage - Woodworking
from John Heisz - I Build It https://www.youtube.com/watch?v=cwY2MN5VD8E
Building a Camper - Solar Set Up, Insulation, Windows
from Laura Kampf https://www.youtube.com/watch?v=jOxFt5LjxjI
2020年6月20日星期六
Shop Made Drawer Pulls
Important workbench maintenance tasks you should be doing
from Stumpy Nubs https://www.youtube.com/watch?v=tkAtZd9RZdA
2020年6月19日星期五
Case Hardening in Wood – Tension Set
Five Quick and Easy Woodturning Finishes
One of woodturning’s attractions is that a beautiful object can be turned in a relatively short period of time. So turners tend to like finishes that beautify and protect their handiwork, pronto. In that spirit, here are some of my choices for quick, simple finishes to try.
Shellac
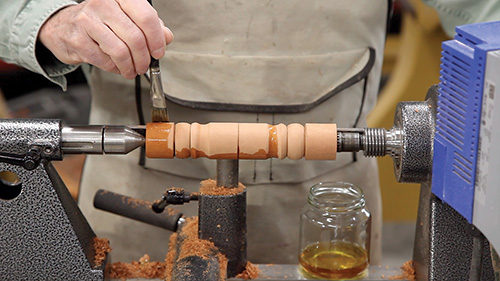
it’s still on the lathe and stationary.
Shellac is a splendid traditional finish for spindle turnings, bowls and boxes. Any finish will stick to shellac and vice versa. It also dries incredibly quickly and is food safe.
While you can buy premixed liquid shellac at a hardware store, I prefer to use dry shellac flakes that have to be dissolved in denatured alcohol. This “old school” shellac will give much better results at the lathe. I mix a small amount of dewaxed shellac flakes with enough denatured alcohol to cover them. I cap the container and let the flakes dissolve over a period of 12 to 24 hours. You can accelerate the process slightly by placing the bottle in a sunny window or outside on warm summer days. This will yield a super-saturated solution — what finishers call an “8-lb. cut,” which equates to 8 pounds of shellac dissolved in one gallon of alcohol.
A full-strength solution like this is far too viscous for our needs and must be diluted by mixing one part full-strength shellac to three parts alcohol. This reduces it to a 2-lb. cut, which is about right for a simple padding application on the lathe.
With the turning mounted in the lathe and stationary, I brush on the shellac. When the wood is completely saturated, start the lathe and burnish the finish with either shavings from the floor or a small piece of paper towel. You need quite a bit of speed for this process to work. I use 1,800 rpm for any spindle between 1/2″ and 2″ in diameter. I increase the speed for parts thinner than 1/2″, and I decrease the speed for turnings over 2″. Let common sense be your guide here.
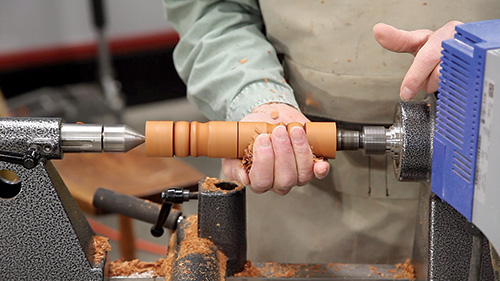
The friction of the shavings or paper causes the alcohol to evaporate, and the shellac melts into a smooth finish. A second coat followed by burnishing and even a third is good measure. Much depends on the strength of the shellac and the wood you are finishing. Open-grain woods will take more coats than close-grained varieties.
Be sure to insulate your hands with sufficient shavings or paper towel to prevent burns, and remove the toolrest to avoid pinches.
If the finish doesn’t seem to build well, your shellac mixture is too thin; add some full-strength liquid shellac to it. If you are getting streaks with chips sticking to the work, the solution is too thick. Add more alcohol.
Carnauba Wax
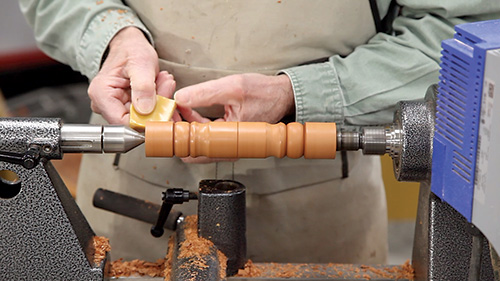
Pure carnauba wax is a fine finish in its own right. It’s a quick finish I use by itself for handles, boxes and turnings. Carnauba is the hardest of waxes and comes from the leaves of a Brazilian palm tree. It is so hard that it cannot be applied in its natural form. It’s an ingredient in many automotive waxes, furniture waxes and friction polishes for turning. These all have various forms of mineral spirits as a vehicle to apply the polish. Once the spirits evaporate, the wax can be buffed out.
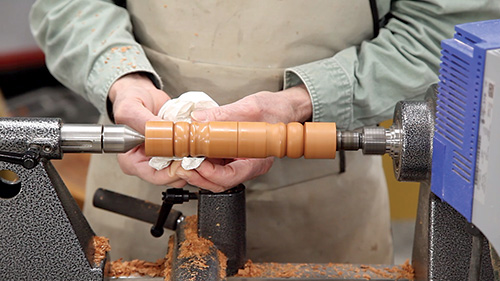
At the lathe, pure carnauba in solid form is a friction polish par excellence, but you must use sufficient speed (per the speeds for shellac, above) to apply it. Hold the wax against the turning to coat the wood, then use chips or paper towel to melt it into a smooth, glossy coating.
Blended Oil Finishes
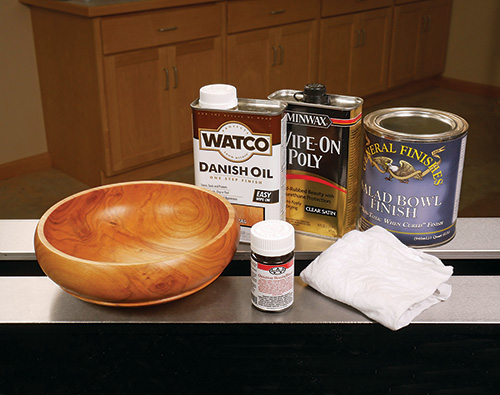
Like shellac, traditional oil finishes have been around for a long time. You can make your own by mixing equal parts of an oil-based varnish, a drying oil such as tung or boiled linseed and mineral spirits. While I’ve tried this homemade brew, I feel premixed commercial examples work just as well and save you the labor.
My favorite commercial oil finish these days is Waterlox Original Sealer Finish — a tung oil-based coating made in Cleveland. Other oil finishes that work well are Minwax Antique Oil (a linseed-based oil finish) and the widely available Watco Danish Oil.
Oil/varnish blends like this polymerize into a hard, durable coating within 24 hours. They have a healthy appetite for oxygen, which is what is needed for them to polymerize. Therefore, a can of oil finish either has to be decanted into smaller containers or used within a day or two to prevent the mixture from beginning to cure. Heat is released in the polymerization process, making this finish potentially flammable if rags are wadded up tightly after use. So, take great care to spread them out flat until the finish dries, and be just as cautious about throwing away brushes and wood shavings saturated with the wet finish. A fireproof metal trash can is a sensible safety measure to add to your shop if you plan to work with a lot of blended oil finishes.
Oil/varnish finish is a great coating for bowls. It can be applied to a bowl that has been turned from unseasoned (green) or dry wood. Since it will inhibit water loss from the end grain, a rough-turned green bowl will dry more evenly, and less checking will occur.
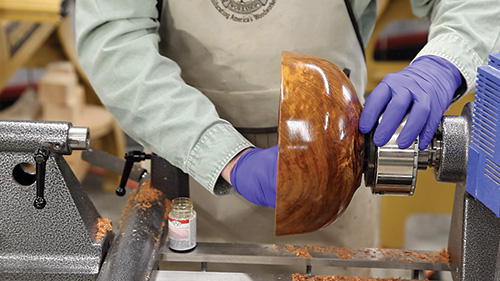
I use blended oil finish for most of my bowls. Once I have sanded a green or dry bowl up to 180-grit, I wipe on the first coat of finish. Then I sand the bowl with 180-grit again. Wet finish actually makes the sanding process more efficient, because the mixture of wood dust and oil fills the wood pores and then hardens into an ideal wood filler that perfectly matches the wood. Burnishing the applied and sanded finish with wood shavings enhances the pore-filling process.
I sand subsequent coats of finish into the wood at 24-hour intervals with progressively finer sandpaper. I use 220-grit for the second coat and 320 for all subsequent coats. Depending on the intended use and the wood the bowl is turned from, I apply anywhere from three to five coats of finish.
It’s handy to keep the bowl on the faceplate for the entire finishing process, which works better for dry wood bowls that aren’t inclined to warp. This doesn’t work as well with green bowls that will continue to distort in the hours following turning.
In terms of food safety issues, be sure to check the safety data sheets for whichever finish you choose. Waterlox’s data sheet, for instance, says that the finish is food safe after 30 days of drying subsequent to the last coat applied.
Walnut Oil
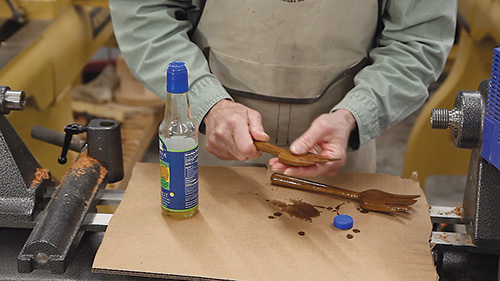
If you want an absolutely food-safe finish, it’s hard to beat walnut oil. You can find it at most grocery stores. In fact, I use my leftover walnut oil as a salad dressing — that’s how safe it is.
Walnut oil is my go-to finish for treenware and bowls that are intended to be used. Application is child’s play too: just pour some on the object to be finished and rub it in with your hands, then wipe off the excess. Although the object can be used immediately, it’s better to wait three or more days for the oil to soak in and begin to dry. Walnut oil will dry eventually, but it is slow to polymerize and does not form a very durable coating. However, you can recoat any time you wish to good effect, whenever the wood begins to look dry.
No Finish at All
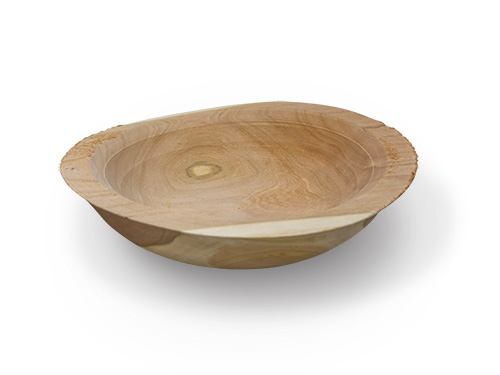
That’s right, no finish at all is often a great option for turned objects. Bowls and treenware were seldom finished in antiquity.

Cooking oil and washing by hand will soon build an attractive patina that will enhance the character of your turned projects permanently.
The post Five Quick and Easy Woodturning Finishes appeared first on Woodworking | Blog | Videos | Plans | How To.
from Woodworking | Blog | Videos | Plans | How To https://ift.tt/2YeXKdy
Bone Damascus Chopper | Knifemaking
from Black Beard Projects https://www.youtube.com/watch?v=CTJ-s2C7X-Y
STL218: Megan Fitzpatrick’s favorite tool storage
from FineWoodworking https://ift.tt/3deVnM7
Free Videos for Father’s Day
from FineWoodworking https://ift.tt/2Yf62C5
2020年6月18日星期四
Free webinar: Tools and the furniture maker with Allan Breed
from FineWoodworking https://ift.tt/37Ht33O
How to accurately set your table saw bevel angle
from Stumpy Nubs https://www.youtube.com/watch?v=8JebPTBB8wI
Recommended resources: Fundamentals of Handplanes
from FineWoodworking https://ift.tt/2UWC9o2
Recommended resources: Limbert Inspired Coffee Table
from FineWoodworking https://ift.tt/3hCoVXs
Recommended resources: Garden Chair
from FineWoodworking https://ift.tt/2YRhBih
Recommended resources: Federal Side Table
from FineWoodworking https://ift.tt/3hFqWlA
Recommended resources: Building Custom Picture Frames
from FineWoodworking https://ift.tt/2UUNBAT
Recommended resources: Build an Elegant Side Table
from FineWoodworking https://ift.tt/3eclLaI
2020年6月17日星期三
Abrasive Cleaner Holder
Synthetic wine corks work great for cleaning abrasives. But all it takes is accidentally bumping your fingers against the spinning sandpaper once, when the cork slips or wears down too far, to want some sort of a holder for the cork that makes this task safer.
Here’s my solution: I insert the cork into a 4-1/2″-long section of 3/4″ I.D. PVC plumbing pipe. Wine corks usually have an outside diameter of about 13/16″, which makes a good friction fit inside this “handle.” It’s a simple fix that saves my skin!
– Jim Wilson
San Marcos, Texas
The post Abrasive Cleaner Holder appeared first on Woodworking | Blog | Videos | Plans | How To.
from Woodworking | Blog | Videos | Plans | How To https://ift.tt/2UUE5NV
Table saw not working right? The proper way to adjust/align it...
from Stumpy Nubs https://www.youtube.com/watch?v=tNfvtStKkFA
Tie Downs & Stuff - Urban Logging Trailer Build Pt 8
from Matthew Cremona https://www.youtube.com/watch?v=n-FmxEjJKlQ
Using SketchUp to Create Patterns
from FineWoodworking https://ift.tt/3hvaZhQ
How long does wood take to dry (faster than I thought it would)
from Matthias random stuff https://www.youtube.com/watch?v=kcGUGS4AaI8
2020年6月16日星期二
Painting Outdated Oak Cabinets
Many houses and condos feature simple builder-grade oak cabinets. They’re inexpensive, simple, unobtrusive, and very “vanilla” so they won’t clash with appliances or other accessories one might add to a kitchen. But for those who wish to make their kitchen look a little more stylish, the outdated oak cabinets just don’t cut it. You guys probably know by now that I’m not real big on paint in general. I like to build with quality hardwoods and I use finishes that enhance their natural beauty. But in this case, we’re talking about mass-produced oak consisting mostly of sheetgoods. Furthermore, these cabinets are in my mom’s new condo and she really likes the painted look, so I’m going to make her happy.
To Pore Fill or Not to Pore Fill?
Oak is an open-grained species so if you just slap on a coat of paint, the pores will telegraph through the finish and you won’t have a smooth appearance. This isn’t necessarily a bad thing, depending on your preferences. In our case, my mom wants the doors to have a smooth appearance so we’re pore-filling. The filler I use is Timbermate. This stuff is usually used as a putty and is very thick but it’s also water-soluble, so you can simply dilute it until you have a spreadable loose pancake batter consistency. Most times, one coat is all you’ll need. After the filler dries, the excess is sanded off and the only filler left on the doors and drawers is the stuff that’s packed into the grain. Just FYI, I did not do the pore-filling process on the face frames and cabinets inside the house. It’s a VERY dusty procedure and most of the face frames are covered by doors and drawers.
Paint
There are a TON of paint products on the market that would work on cabinets. Since I rarely delve into paint, I’m sticking with the materials I’m familiar with and that’s General Finishes Milk Paint. In spite of its name, this paint is actually an acrylic blend but provides the matte look that’s associated with traditional milk paint. Even though it’s more durable than the traditional stuff, it should still be top-coated with something like General Finishes High Performance if it’s to be in a high-use environment.
I used a turbine HVLP system to spray the doors and drawers and a brush and roller to paint the face frames and cabinets. I chose not to paint the cabinet interiors. If you do paint the interiors, consider the wear and tear of dishes and glasses and that the surfaces might look pretty bad after a while.
Stuff I Used:
- Timbermate Wood Filler
- General Finishes Milk Paint – We used Linen and Dark Chocolate
- General Finishes High Performance (Satin)
- Fuji Q5 Turbine Sprayer
- Fuji Semi-Pro 2 Turbine (a more budget-friendly option)
- Rubber Sanding Grips
The post Painting Outdated Oak Cabinets appeared first on The Wood Whisperer.
from The Wood Whisperer https://ift.tt/3hyIyzv
Not Expecting That…
Once again the Weekly faithful have surprised me. Last week, I confessed that I am about to build a ukulele for my granddaughter from a kit. I expected to be called out as a woodworking fraud and have my “workshop card” recalled.
To be fair, a few of you have let me know that, in your opinion, kits are not woodworking (see Feedback in this issue). But a surprising number of readers have expressed the opinion that a kit is a good way to attempt a new aspect of woodworking. Kits definitely have their place — especially for building things like musical instruments and boats.
So I am relieved to retain my woodworking credentials, and I will let you all know how the ukulele project unfolds. Apparently, even old dogs like me can learn some new tricks.
Rob Johnstone, Woodworker’s Journal
Circle-cutting Jig with Fine Adjustment
This jig allows you to cut out or shape accurate circles, semicircles and arcs using a standard jigsaw or router.
VIDEO: Six Things to Know Before Buying a Jointer
What should you consider when you’re shopping for a woodworking jointer? Your budget is an obvious consideration, but there are also six features or options that are important to consider, including the board capacity, the cutterhead style, the fence, the type of infeed and outfeed table lifts, if it has casters or a mobile base, and the drive belt tensioning system. In this video, Chris Marshall goes over the pros and cons of different options available.
From Our Sponsor
Here’s an economical way to help sustain top table saw performance – make your own zero-clearance throat plates! Learn the steps in our handy Skill Builder video below. |
15% OFF: Excludes gift cards, product bundles with gift cards or free products, power tools, Porter-Cable dovetail jigs, CNC machines, Leigh products, SawStop, Festool, Tormek, Ready2Rout, select Rockwell products, taxes, Apollo sprayers, shipping charges, sale items and other promotions. Other exclusions may apply.
FREE SHIPPING: $39+ Orders. Additional shipping charges will apply for select oversized items, express orders, international orders, and orders to Alaska, Hawaii, Guam, Puerto Rico, and the Virgin Islands. Rockler reserves the right to limit quantities, correct errors or omissions and modify or end this promotion at any time. Neither 15% off nor FREE SHIPPING can be combined with any other offer or applied to previous orders. Not valid with Rockler’s Professional Catalog and independent resellers. Offer ends 7/2/20.
The post Not Expecting That… appeared first on Woodworking | Blog | Videos | Plans | How To.
from Woodworking | Blog | Videos | Plans | How To https://ift.tt/2N0DN3X
Workshop Tip: Trim edge banding on the router table
from FineWoodworking https://ift.tt/2N5TF50
Don’t take my word for it
from FineWoodworking https://ift.tt/2YEhtT9
Building from Kits: Yea or Nay?
Last week, Rob shared that he plans to build a ukulele from a kit and wondered if kits are a legitimate form of woodworking. Many of you say you fully support “pre-packaged” project kits. – Editor
“I built a ukulele for my granddaughter using the Tenor Ukulele Kit from Rockler. Everything needed was in the kit. Although it was challenging, the final product came out very well. She loves it and I don’t think I would have had the patience to make it without a kit.” – Red Mulvanny
“I found a kit to be a great way to share my woodworking experience with my grandson. About 15 years ago, I purchased a guitar kit and worked weekends on it with him (at the time he had been playing for several years and wanted a personalized guitar). I was thrilled, as he’s the only one of five to be interested in handiwork, to share with him how to plan, assemble and select colors and finish treatment for the instrument. In other words, an entire project from start to finish. He is now a construction manager with lots of skills and an enduring appreciation for wood and construction — all begun for about a hundred bucks. Priceless!” – Larry Leighton
“I just finished this soprano ukulele kit build that I received as a 60th birthday gift from my sister. I felt that the kit was the best choice for me, just to get the gist of it. Hope that makes since! Everything is right there. I felt that the quality of the kit was good. I now know what the inside entails and I feel very confident that I can tackle the next one on my own. I don’t feel I cheated in any way! When my friends say, ‘Wow you made that!’ I do admit that it was a kit but I added a little inlay… I also just gave it several coats of Danish oil and then lacquer. I like the finish. The next one I build will have banding, more inlay and perhaps a rosette. I also made templates of all the pieces, so voila to the next one! Whatever you decide to make, Rob, pick up a clamp-on tuner so she can start tuning and play it right away. If you have made a guitar already, that’s what you should make for her after the ukulele kit! What a lucky girl!” – Claudia Fletcher
“I have used kits for sheds as well as built them with just plans. As far as I can tell, the only difference is that the pieces are precut and you don’t have to go shopping for the right parts and wood. You still need woodworking skills that can range to the advanced if the kit is difficult.” – Katheri365
“I’ve not had any first-hand work with kits to make musical instruments, but a relative of my wife did make a violin that his daughter played at the funeral of an aunt. It really sounded great! I hope this will give you good feelings about your endeavor.” – J. Eric Pennestri
“I also built a uke kit for my granddaughter. I have some woodworking experience, and I also considered building one from ‘scratch’ but abandoned that idea, based on the need to bend the side pieces. Building the kit went very well, but it’s not without challenges and the need to have various tools not common to non-woodworkers (lots of specific clamps and even a router — preferably a table mounted one). I would strongly advise anyone considering a kit to first review the instructions. This is not like building a plastic model airplane kit. The kit I built utilized veneered top, bottom and sides. The veneer was very thin and discouraged much sanding prior to finishing. They now offer solid-wood kits. Although they are pricier, I would recommend them. It would simplify the build and probably yield a higher-quality ukulele.” – Bill Lebel
“I am on my second guitar kit build. I think the biggest lessons you can learn with a guitar kit are about finish work. Yes you can get into building the entire guitar body and neck and that is pretty technical, but the finishing of these guitars has taught me so much about staining, finishes and how they interact with each other. Above are photos of a bass guitar I did from a kit and the one I am working on now, which is a Les Paul style.” – Jay Stephens
“Though I have no experience with musical instrument kits (I have no talent there), I build wooden models of fire trucks, excavators, tractors and such, and I find the instructions and plans helpful in learning new techniques, such as how to put treads on tractor wheels. Recently I built a model bluenose schooner. Without the kit’s plans and instructions, I know I could never have finished it. So for plans, my vote is yes.” – John van Veen
“I would be interested in a DIY sailboat kit — one with remote-control power included.” – Joe Zwack
“I think kits have their place, especially for something complex that you have never done before. They basically take advantage of someone else’s experience. However, I don’t think I would use a kit for the second one I make. You should be able to learn enough from following their construction to repeat it yourself. The exception to this might be if special machinery you do not possess and that does not make sense to purchase might be needed to make accurate parts. Kits can also provide confidence to those not yet confident in their abilities and can serve as a stepping stone to better projects and more confidence. Personally, I do not use kits anymore nor do I buy plans. I now look at something and do my own version with my own drawings. For me, the design process is as rewarding as the execution, and I love making each piece unique to fit my skills or push me to learn new ones. That being said, if I were asked to make a ukulele, I would probably go to a kit as I have never attempted a musical instrument, and they seem pretty exact.” – Tom Shapley
“Many years ago when I was a fairly young man, which I am not now (76), I had limited time, tools and skills. I wanted to give my spouse a grandmother clock for Christmas. Rather than building it from plans, I took the easy way and purchased a kit. All of the pieces were precut, and there were a lot of miters! I followed the instructions step-by-step in assembling the clock, then stained and finished it with oil. It turned very well and is still working after 40+ years (although the works had to be replaced). When daughter #1 got married, I purchased the kit for their wedding present. Same for daughters #2 and #3. When my youngest got married, she requested the traditional wedding clock! So, that is five kits! I like making things from scratch, but for something like this, the kit was great. I would not have tackled the clock without a kit. My only regret was not buying five all at once — the price from #1 to #5 went up by three or four times! If the fifth daughter should marry, and I doubt she will, I’ll order kit number six, even though I have the tools and time and have developed the skills to do one from scratch!” – Karl Reichardt
“I made ukuleles from a kit several years ago for Christmas. They turned out great. A violin didn’t do as well, but they all look great.” – Barney Heller
“Kits have their place in woodworking from a number of perspectives. Using a kit for a full-featured workbench can save time and money going through the iterations from working on the floor through sawhorses and so forth until you have the pilot workbench to use to build your dream. Using a kit for a ship model can speed the process to producing a decorative piece without having to acquire hundreds of one-off tools and materials. The kit question also bears on how far you go back with prep work. Fancy growing your own timber? Making all your own tools? Inventing your own adhesives or finishes? On the other hand, there are some things for which there are no kits. I have found that I can make lathe benches that are much more effective at dampening vibration than the off-the-shelf models, by sloping the legs and making them to exactly the right height for the lathe owner.” – Graeme Coles
“It’s not like you are building a birdhouse from a kit. (A ukulele kit) should be a good experience and worth a few lines of print. Stay unconfirmed.” – Doyle Moeller
“I made my wife a ukulele (pictured above) from a video. I had no experience with building instruments but it turned out sounding good — good enough that she has played it at her ukulele group where she regularly plays her Kala concert model. It is a box-type soprano size — Baltic birch, mahogany, cherry neck, bubinga bridge and a snakewood nut and saddle. The scariest part is waiting while it is finally tuned and strummed; if it doesn’t sound good, then I just made a wall ornament. Whatever way you go, good luck and enjoy the process.” – Ron Bailey
“My late wife bought me a kit for a mandolin, one that would be a Red Diamond if built by them. It was a high-end kit that the manufacturer said would take a lot of woodworking skills. My wife assured him that I could build anything out of wood — don’t know quite where she got that idea…Anyway, it did demand a lot of skills and tools that I had to learn and acquire over the course of building it. I started in 2010 and would work on it until I got to a point where I thought I was going to mess it up, so I would stop, get some more tools, do some research and then proceed to the next step. Finally in 2013, I decided that I was going to finish it, right or wrong, and I worked on it every night from January 1 to around April 12, when I tuned up the first string. The sound was extraordinary in my opinion, and I couldn’t wait to let my brother, a self-taught and accomplished guitar player, help me string it up the rest of the way the next morning. He was ecstatic also. He even tried to borrow it from me to take the Galax, Virginia, fiddlers convention to show it off to a bunch of musicians he knows. That said, I would not have been able to build it without a kit. It took well over 120 hours of work from start to finish, but it is a treasure to me, and I get many compliments on it. I think I could build another one in around 80 hours from a kit, but don’t know if I could make one from raw wood. Good luck. I am building a dulcimer from a kit now.” – Mark Carnes
“It might not take as much skill with a kit, but it still requires patience and pride in what you are doing.” – Doug Ellis
“I enjoyed making several clocks from kits. Then I got more tools and made a number of small household items with my grandchildren. Now I’ve put my house on the market and will move to a condominium apartment. If I want to be creative with wood, I’ll have to use kits again.” – Alan Stein
“I have done both from kit and from scratch. They are fun, and good plans help a lot. I made the above hammered dulcimer from scratch for about $250, using a set of plans. It was great fun and is a beautiful piece. The plans were great. These instruments sell for around $1,000. I think it looks very nice in my dining room.” – Phil Zoeller
“I’ve made several things from kits. As someone who works on average 60 hours a week and has limited shop space (a garage when I move the wife’s car out of it), a kit can come in very handy. Assembling and finishing are often the real keys to making a project shine, so that part is not lost. I made both of my daughters jewelry boxes as well as display cabinets from scratch, based on a picture of the display cabinet that they sold as a kit. I’ve also made a lot of furniture from scratch, and I think whether you build from a kit or from scratch all depends on how much time you have available. The key is just to be making things.” – Frank McEnulty
“I have never built any wood items from a kit. But I also build high-powered model rockets, and I’ve built many of them from kits. It’s much easier to get someone else to source all that fiberglass, tubing, etc.! However, I’ve seen several toy kits (cars trucks, bulldozers, etc.) that caught my eye and interest. Still, having no grandkids at this point in my life, I just kept on walking. As for guitars and such, I already have several, so I’ve never really thought about it much. Maybe if I win the lottery and can afford to buy a nice CNC…” – Steve Kendall
But kits are thumbs-down for a number of others. – Editor
“Kits limit creativity and don’t stretch your abilities. Mistakes hone your skills.” – Tom Moss
“Taking the kit route is a copout for building a uke or guitar. Every kit I’ve seen is a waste if money. End product will be mediocre at best. I can make a uke from a cigar box that will beat any kit at a quarter the cost, and the quality will be better.” – Chris Jenkins
“If you’ve built guitars without a kit, a uke is a piece of cake. No need for a kit unless you are really pressed for time. My opinion is that you didn’t really build it if you bought a kit. Sorry.” – Frank Clements
“I really hate kits. But if I were to be making a uke, I would have to buy a kit. I don’t have all of the equipment to do the job from scratch.” – Lowell Taylor
The post Building from Kits: Yea or Nay? appeared first on Woodworking | Blog | Videos | Plans | How To.
from Woodworking | Blog | Videos | Plans | How To https://ift.tt/30YZABl
2020年6月15日星期一
No more dusty and messy bins to empty!
from FineWoodworking https://ift.tt/2CdhAxv
AAW Announces Virtual Woodturning Event July 10-12
from FineWoodworking https://ift.tt/37xhs7n
A simple way to rout miter slots
from FineWoodworking https://ift.tt/2Y5WVE2
2020年6月14日星期日
Bike Wall Hanger Dropzone
Video Tutorial
Please take a second to watch our quick video tutorial to see how this bike rack shelf is made.
from Recent Project Plans https://ift.tt/2N0RG21
How To Make Sanding Drums The Easy Way
from John Heisz - I Build It https://www.youtube.com/watch?v=NFkTR_jfulA
2020年6月12日星期五
Marc’s Meat Sweats
00:00:32 – Video starts
00:01:18 – Welcome to the WoodWhisperer Morning Show
00:02:00 – Thanks to our new Patreon subscribers
00:02:58 – Mail time! Thank you, Nerd with Wood!
00:04:28 – Thank You Lower48 Woodshop!
Recommend an Instagram or YouTube Channel to us here
00:09:30 – Marc’s BBQ Instagram account
00:11:20 – All Wood Whisperer episodes are on Amazon Prime! https://amzn.to/3hoJWof
00:12:12 – How much does bent lamination spring back when removed from the form?
00:14:20 – What hardwood did you use for the trim on shop cabinets?
00:15:14 – What are your thoughts on bringing in a bandsaw as one of the first big power tools?
00:18:00 – Any suggestions for getting a better finish from a drum sander?
00:20:10 – Is a hollow chisel mortiser worth the floor space if you have a domino?
00:23:40 – How can you optimize storage in shop cabinets?
00:25:30 – Can you use the 5 cut method to dial in a table saw fence?
00:27:35 – Have you ever used oil-based stain?
00:29:45 – Expansion on the 5 cut method answer
00:31:55 – Do you ever design on the fly?
00:33:20 – What are some resources to get started in furniture design?
00:36:07 – How much paint do you need to use before you get good coverage on the hall tree?
00:38:40 – How can I find information on my local woodworking group?
00:42:05 – Do you have any resources for learning how to BBQ? Resource 1, 2, 3
00:46:20 – Is there a wood you wouldn’t use for loose tenons?
00:47:20 – Should I use a food-safe finish on a chessboard?
00:48:20 – What should my order of operations be when assembling a cedar chest?
00:49:20 – Maybe he meant cheese board?
00:50:20 – Can I create a faux shiplap look out of plywood?
00:51:22 – How can I reduce tear-out from cutting miters?
00:53:13 – What’s your policy on lending out tools?
00:55:00 – What grits would you recommend on sharpening with diamond stones?
00:56:15 – Do you use the table that came with the drill press or do you have an aftermarket one?
00:57:25 – Would you consider making a video of your average workday?
00:58:50 – Nicole, when did you start letting Marc build furniture for your home?
01:02:15 – Is the Anarchist Design book any good?
01:02:45 – Guild project winner! Congratulations!
The Wood Whisperer Guild gift certificates:
No show next Friday
Searchable Spreadsheet for The Wood Whisperer Morning Show Q&A
Want to learn more about us?
Check out our free videos at TheWoodWhisperer.com
Catch up with our recent charity efforts at WoodWorkersFightingCancer.com
Join the Wood Whisperer Guild by purchasing one of our courses.
If you like what we do and you want to see more of it, please consider helping us out by becoming a Patron. We truly appreciate your support!
https://ift.tt/2gRui6g
Looking for the products and tools Marc uses and recommends? You can find them at our Amazon stores:
US – https://www.amazon.com/shop/thewoodwhisperer
Canada – https://www.amazon.ca/shop/thewoodwhisperer
UK – https://www.amazon.co.uk/shop/thewoodwhisperer
The post Marc’s Meat Sweats appeared first on The Wood Whisperer.
from The Wood Whisperer https://ift.tt/37qz5ps
DIY Stacked Cork And Resin Material
from Black Beard Projects https://www.youtube.com/watch?v=jd4qiTlsJg8
How To Make A Power Hacksaw Machine || DIY Power Hacksaw
from Mistry MakeTool https://www.youtube.com/watch?v=64DGWUvmzfc
Four Wild Windsors
from FineWoodworking https://ift.tt/2B14mTS
50 Amazing Fastest Woodworking Projects Techniques Ideas Tools Wood DIY Simple Easy Creative Craft
from UWOODWORKER https://www.youtube.com/watch?v=9ykplD5zNeQ
2020年6月11日星期四
Tool Review: Onieda’s Super Cell Dust Collector
from FineWoodworking https://ift.tt/2AWEOY3
Cutting Bowl Blanks from a Tree
This article, “Cutting Bowl Blanks from a Tree,” by Dale Larson, is from the pages of American Woodturner and is brought to you by the America Association of Woodturners (AAW) in partnership with Woodworker’s Journal.
There are many ways to cut bowl blanks out of a tree, but the methodical approach that I take efficiently uses the tree and produces stable, aesthetically pleasing bowl blanks. If you have a chainsaw and are willing to put it to work, I will explain how to evaluate a tree to determine where the best bowl blanks lie in wait. On the other hand, if you buy bowl blanks, my approach will improve your skill at evaluating the opportunities within the stock available for purchase. The goal is to predict what your finished bowl will look like before a gouge even touches the surface of the blank.
Timing Is Everything
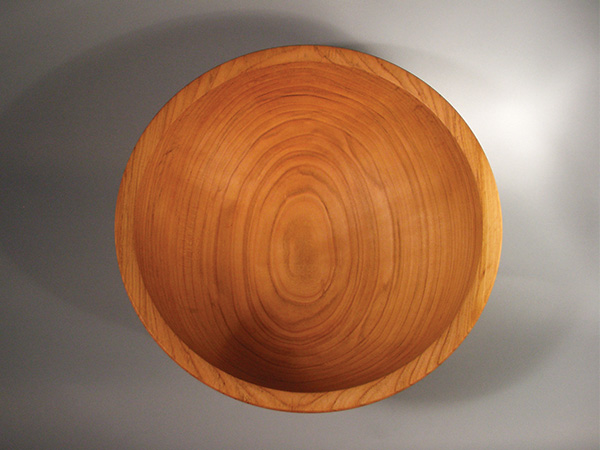
When I get green wood, it becomes my top priority until I get the subsequent blanks rough-turned. Unprocessed green timber never improves with time. The longer the log sits, the more cracks it will develop, fungus will move in and cause discoloration and loss of luster, and insects will tunnel into the wood. For the log I processed for this article, I cut the blanks on a Thursday and rough-turned them the next day, and this was during a relatively cool and humid part of the year. I use an emulsified wax solution (Sealtite 60) during warm weather to coat the endgrain as soon as I make the cut. I will also spray water on the blanks and cover them with a tarp until I can rough-turn them. In my experience, a cherry bowl blank cut in July will show visible cracks within an hour. If the blank checks, I will have wasted my time in locating the wood and cutting it up.
Chainsaw Safety
While the steps in this article rely on a chainsaw, detailed guidelines for the safe use of this both helpful and dangerous tool are beyond the scope of this article. Several articles related to chainsaw safety have been published including this one by Sandor Nagyszlanczy. The price of using a chainsaw without appropriate precautions can be high, even deadly, either for the saw operator or observers who are too close to the action. When I am using a chainsaw, no one is allowed to be close to me or to hold the piece of wood I am cutting.
Prioritizing the Cuts
I almost always start by cutting up the most valuable—meaning highly figured—part of the tree. If the tree has burls, that is where I focus my initial efforts. I cut the crotch pieces next, followed by the lowest part of the trunk where it transitions to the stump. I then work my way up the trunk, leaving the limbs for last. Limbs are full of stress and typically have both the poorest figure and the poorest turning quality. My theory is that if the chainsaw gives up before I do, the best wood from the tree should already be in the back of the pickup.
Dissecting the Tree
The yellow poplar in the accompanying photos lies in my driveway, and knowing I have ample time to finish the task, I decide to cut the straight-grain blanks first. Measuring the tree’s diameter, I decide to make 14″ (36cm) bowl blanks. I slice a few inches from the butt of the log to remove any checking and to help clarify the grain pattern. I then cut the first round 15″ (38cm) long, which will provide leeway to bandsaw the blank to its final 14″ diameter.
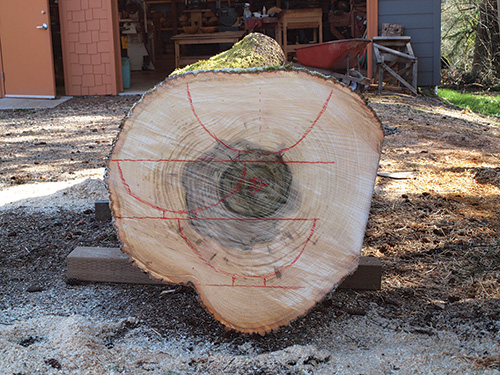
A stable section for a utility vessel requires leaving the pith out of any blank. Checking originates from the pith, so excluding this area eliminates a reliable source of stress in the wood. With that in mind, there are three basic orientations for blanks from straight-grain wood. I have roughly marked the grain lines to illustrate how they are oriented in each blank. The blank on the bottom will yield my favorite grain pattern. It is flat sawn with the center of the bowl aligned with the bottom of the curve of the growth rings. This blank will yield a pleasing, symmetrical grain pattern mirrored in each side of the bowl—a pattern I call butterfly grain.
Quarter-sawn blanks lie on both sides of the pith. For the species of timber that I use, I rarely make quartersawn bowls because, to my eye, the resulting grain pattern is not as appealing—the grain lines run straight through the bottom of the bowl and show little or no curl, eyes, or any of the other variants that make wood visually appealing. The exception is when I can acquire a species with strong medullary rays such as our local Oregon white oak (Garry oak). The grain in quarter-sawn oak can far outshine its flat-sawn relatives.
The top blank in the above photo can be used to make a natural-edge vessel, or the outer edge can be removed for a smooth rimmed bowl. The grain orientation running through this blank will produce an approximately round or oval grain pattern in the bottom of the finished bowl. I usually evaluate the blank and consider whether the outer (bark) edge will yield a balanced shape, and if so I will keep the outside intact for a natural-edge bowl. Here I decide against a natural-edge form.
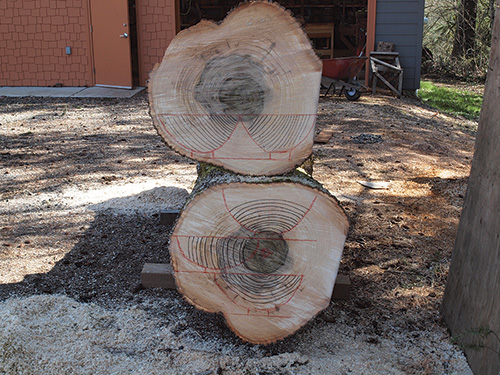
Yet another orientation is possible, an arrangement I call slash-sawn, although the grain orientation approximates rift-sawn dimensioned lumber . The slash-sawn blanks will distort significantly while drying, sometimes to the point of being unworkable, and the finished bowl will simply not be as attractive as the flat-sawn bowl. It is true that more of the log will be lost in taking the one flat sawn blank instead of two slash-sawn blanks. Turner and teacher Lane Philips’ mantra is, “Don’t trade volume for beauty,” and I too encourage taking the best blanks out of the tree, not the most blanks.
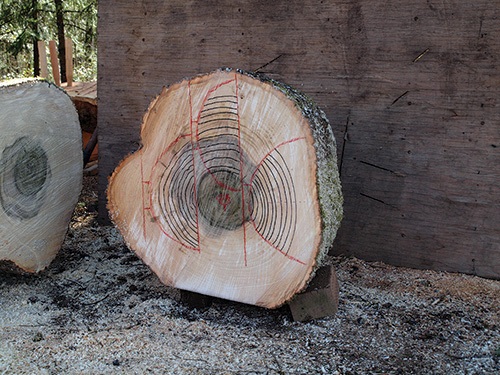
I balance the round on wood blocks to prepare it for cutting, ensuring the round is stable and will not roll during the cuts. I orient the cut lines vertically, as cutting straight down is easier and more accurate than attempting an angled cut. Because most of my cuts are with the grain, I use a rip, or skip-tooth, chain on my chainsaws. These chains also work for cross-cutting and are less prone to clogging from the long curls generated by the rip cut. A secondary benefit of a rip chain is that when it is dull, it has half as many teeth to sharpen as a standard chain.
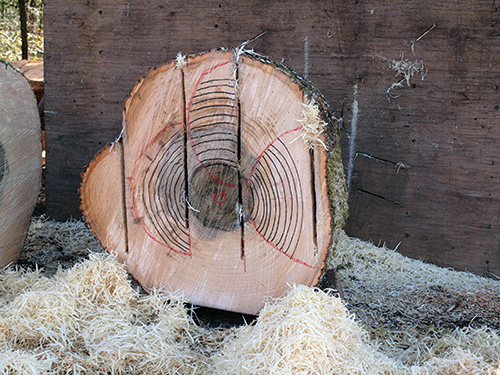
before completing the dissection, working from the outside to the inside cuts.
I make all the parallel cuts, stopping each cut short of exiting the log. Before I make the first center cut, I mark the location of the pith on the far end of the round. This guides my cut to keep it running parallel through the block with the pith line. Having the grain oriented straight through the blank is important to the appearance of the finished bowl. The prettiest bowl pattern has the grain parallel to the bottom of the bowl. If I have to choose between making the cut parallel to the pith line and the bark line, I generally cut parallel to the bark line to preserve the desired grain orientation.
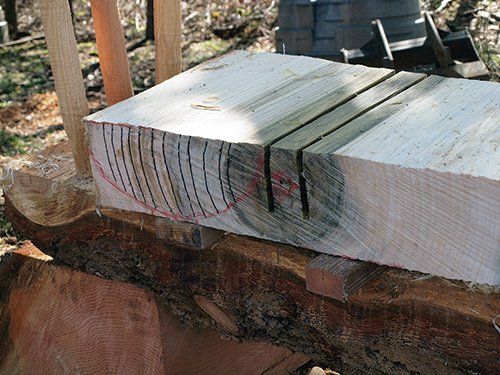
The quarter-sawn blank rests on my cutting bench, a 22″- (56cm-) high jig that minimizes my stooping and saves wear-and-tear on my back. I cut outside the checks around the pith; I will get two quarter-sawn blanks out of the slab. I did not cut through the slab because the support blocks underneath the blank are in the wrong location. A through-cut in this situation could pinch my bar.
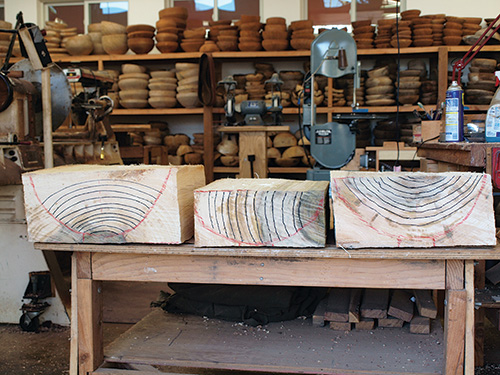
The three basic straight-grain blanks sit on the workbench, bandsaw ready. The flat top and bottom offer two stable surfaces for the bandsaw table. Trying to cut a round or irregular- bottom bowl blank on the bandsaw can lead to an unsupported and dangerous cut.
Cutting the Crotch
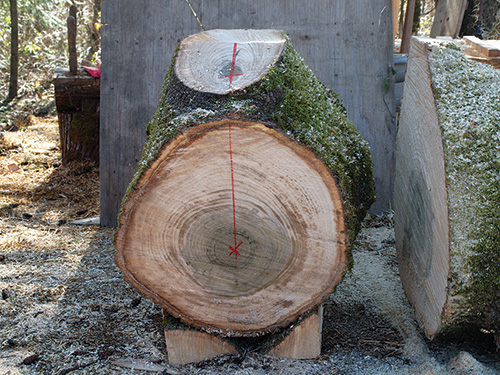
I cut a 15″- (38cm-) round from the tree that includes the crotch section. In the area between the two limbs’ pith lines will lie an expanse of interlocked feather grain, or crotch figure, and I have attempted to cross-cut the log below this region.
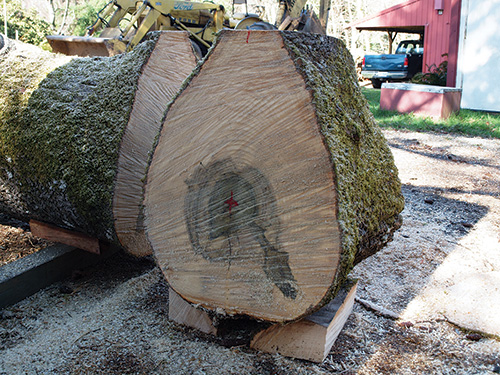
A straight line connects the pith of the limb to the pith of the tree. As with the previous round, I orient this line vertically for cutting. I mark the pith at the end of the round and transfer the mark to the top of the log where I will use the location to guide my cut. I also mark any checking to be avoided around each pith, of which there is little in this log.
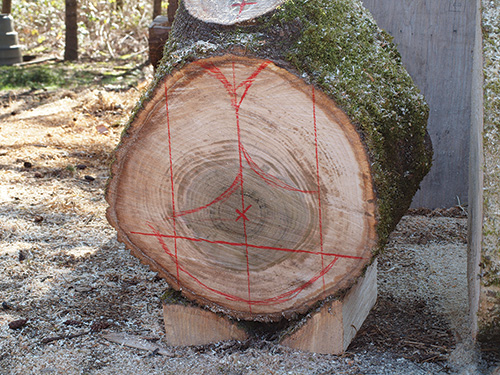
This photo shows the approximate orientation of the three blanks I could extract. If this were expensive or rare wood, I would separate the bottom bowl blank first, but because that blank would be flat-sawn and straight-grain, I decide to forego extracting it.
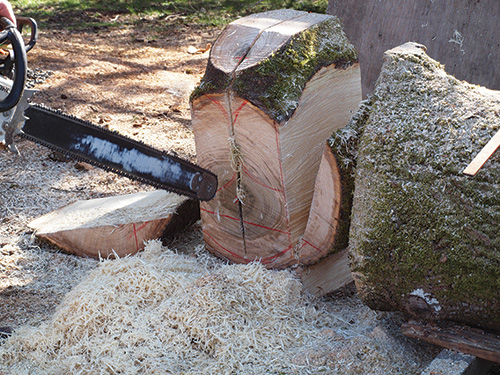
I make the center cut first, stopping short of cutting completely through the log. Then I slice off each side before returning to finish the center cut. I always saw from the upper end of a crotch section where the most prized feather figure lies. The feather will taper off towards the bottom of the cut, so if my cut wanders a little, there is less likelihood of losing the best figure.
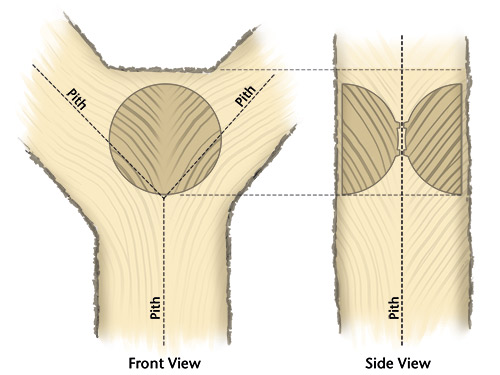
The drawing shows how the feather-figure bowls are oriented in the tree’s crotch. The side view in this illustration shows the location of the pith, which I intend to bisect with my cut. The bowl bottoms are oriented towards the center of the tree, placing the feather pattern in the bottom of the finished bowl.
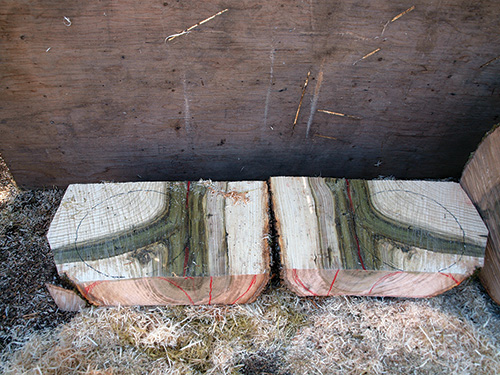
With the crotch section halved, I mark out the best patterns with my calipers and highlight the pith lines with red chalk. Cutting the blanks along the pith lines yields two bowl and two spindle blanks. The feather figure lies above the pith line of the limb and to the right side of the trunk pith line. This crotch did not have a big feather area. Harder to see in the photos is that the weight of the limb has compressed the wood at the junction with the trunk to create fiddleback figure, which I have shaded with a marker.
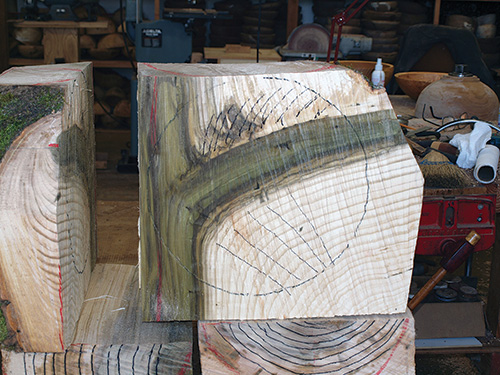
These blanks are now ready to be bandsawed and rough-turned. I will make my final adjustments to the forms for grain alignment as I rough out the blanks between centers, an approach I learned from John Jordan. Turning between centers gives me an opportunity to make final adjustments to the bowl blank and possibly correct mistakes made during chainsawing.
Final Thoughts
There are many advantages to working green wood, including salvaging local timber that may not be commercially available. Cutting one’s own blanks offers the chance to optimize blank size and grain patterns. Turning green wood also generates less dust and requires less physical effort than seasoned wood. Finally, when I rough out green blanks, I get to see colors in the fresh wood that no one else will see. Fresh madrone can be bright red, almost fluorescent, and black walnut can show shades of deep purple and green. Unfortunately, these bright colors fade as the wood dries. With experience processing my own trees, I rarely buy a bowl blank. I find I am no longer willing to give up control of this part of the creative process.
For those who would like to dive deeper into this subject, I recommend two books: Reading the Wood by Michael Elkan and Turning Green Wood by Michael O’Donnell.
Dale Larson has been turning bowls for forty years. He is a founding member and past president of the Cascade Woodturners in Portland, Oregon. Dale served on the AAW Board from 2009 to 2014, as both symposium chair and president.
The post Cutting Bowl Blanks from a Tree appeared first on Woodworking | Blog | Videos | Plans | How To.
from Woodworking | Blog | Videos | Plans | How To https://ift.tt/30wGVwg